Don't blow it off: 5 proven tips for fast, low-cost compressed air savings
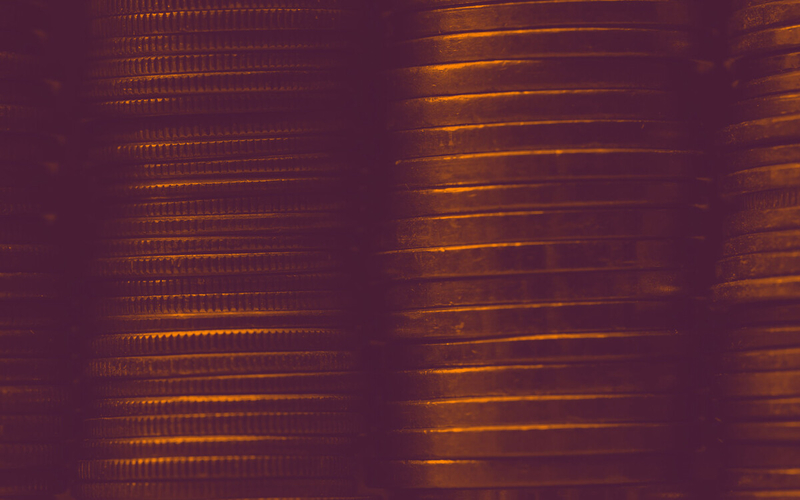
Compressed air is (still) perceived as "free" by some operators at manufacturing sites. With mounting pressure on controlling costs, we often find that opportunities to improve the performance of a compressed air system are often undervalued.
Compressed air systems typically account for 10-25% of total site electricity bill. In our Covid-19 series of articles, we share our experience of some of the most common quick wins, often requiring little effort, to ensure you keep your energy budget under control.
Here are our 5 energy saving actions for compressed air:
1. Investigate what stops you from reducing compressed air pressure.
Reducing compressed air pressure is a common recommendation, often made with little background to the operations. However, we often find this a plausible opportunity in most cases and can be enabled by ensuring that:
- The system is kept leak-free
- The system is condensate free- look for blocked drainage points at low points in the system
- Filters are regularly serviced
- Air receivers are placed in appropriate locations
A common complaint when reducing pressure is that users at the far end of the distribution network are starved of air and therefore pressure is increased to compensate for this. Reviewing the design and the need for air receivers should be balanced against the potential of saving 1% of compressor electricity consumption for every 0.3 barg drop in pressure. What does this 1% mean for your electricity bill?
2. Carry out a visual inspection of compressed air end users.
Compressed air is a versatile energy vector and therefore often used for other purposes than it is designed for- or abused. Typical examples of this are the use of open-ended pipes hastily tidied up, or compressed air hoses to blow off debris in the place of standard cleaning tools, used with little, manual or no air regulation. Consider isolating these supplies in the short term and challenge the status quo. In the longer term, seek for opportunities to replace compressed air with low-pressure air where applicable.
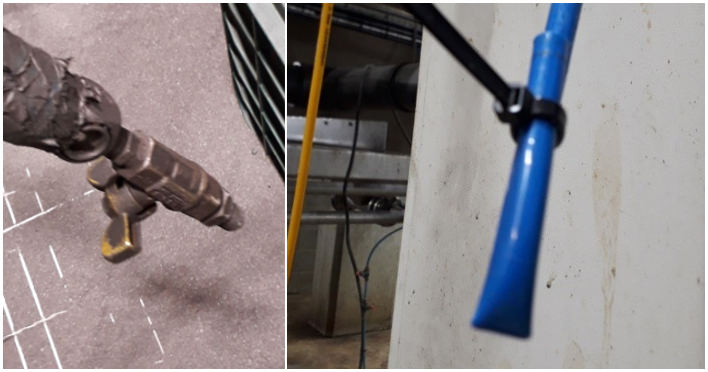
3. Challenge your baseload consumption.
Shutdowns and weekends provide some of the best periods to review baseload consumption and identify inefficiencies including compressed air leaks. The operators can set a benchmark once a system has been audited and leaks rectified (we argued in a previous article that this can be done in house) and target that any baseload consumption should meet this. Below is a snapshot example from a client’s data showing Christmas period compressor baseload and several deviations in consequent weekend baseloads. What does your out of hours and weekend baseload look like?
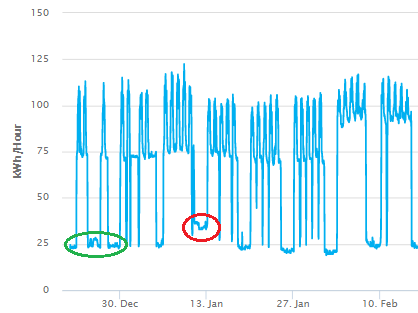
4. Review your sequencing patterns.
At a recent client site visit, we observed that the two site compressors (one fixed speed, one VSD) were rotating duty based on a timer, set on the premise of sharing load and therefore wear over time (a common maintenance consideration). In fact, the fixed speed compressor was consuming 40% more power for the same demand (see following graph), resulting in an unnecessary spend of £6k per year (10% of the total compressed air electricity consumption). The client switched the duty permanently to the VSD as a short-term action and plans for installing a sequencer to control duty on air pressure.
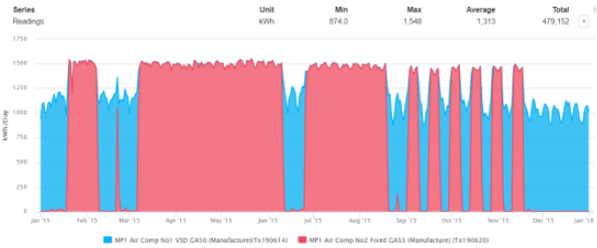
5. Meter your compressor consumption.
Metering your electricity consumption for compressed air generation and (as a minimum) the total volume generated provides insightful information for your system and quick return on investment opportunities to improve performance. These opportunities typically represent a minimum of 2-3% of total site electricity consumption. The effort to install metering on compressors pays back in months and we have seen numerous examples of this via Carbon Desktop. Consider this as a starting point for metering and monitoring programmes, proving savings early in the process.
(Still) Here to help you achieve zero
We are currently offering a free taster bureau report for manufacturers to save energy, including a remote review of your compressed air consumption patterns.
Find out more about the free taster bureau report
Offer ends on 1st July 2020.
Stay safe.
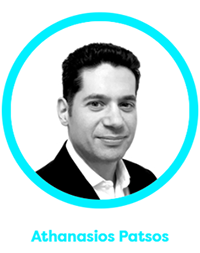