Tips to meet your net zero carbon commitment- An example from the printing sector
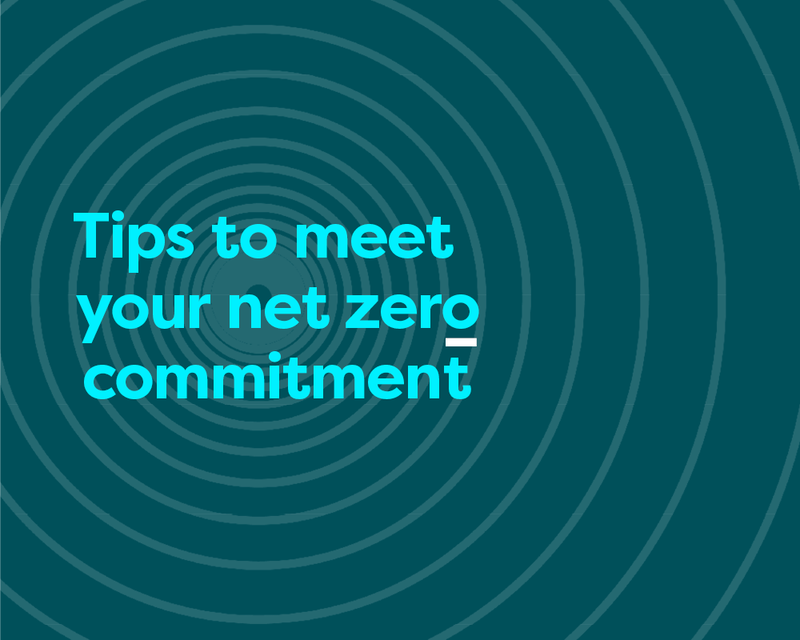
The surge on Net Zero Carbon commitments is now well underway in the Corporate sector with businesses committing to action plans and targets well before the middle of the century. Many businesses are already choosing 2040 or even 2030 commitment years in line with SBTi targets. Verco is supporting a multitude of clients with ambitious Net Zero targets, some of which need to be met as early as the end of 2022!
The UK printing industry alone sees around 8,000 operating companies, employing more than 110,00 people with a significant cumulative turnover of £14bn. Around 50% of the sector is involved in printing on paper, while 20% is carton and label printing, with 5% being high-value security printing.

Despite the relative differences, there are common themes across the entire printing sector owing, but not limited, to:
- The sourcing and use of raw material
- The upstream processing of raw material
- The transport to and from the factory gate
- The energy-intensive nature of on-site operations
This article shares some useful tips and insights for the journey to net zero, illustrated using an example of some of our recent work in the printing sector.
Step 1- Understand your current position and where you can influence change to build your net zero pathway
Carrying out a materiality assessment and assessing your organisational footprint are the first steps. For the example organisation, Verco tailored the approach of the assessment which resulted in taking a “cradle-to-gate” approach recognising the relative importance of emission sources and influence of the business over the lifetime of the product. Over 2/3 of the organisational footprint is down to Scope 3 emissions (Figure 1) and therefore potentially beyond the organisation’s direct control and – one would expect – generally harder to abate.
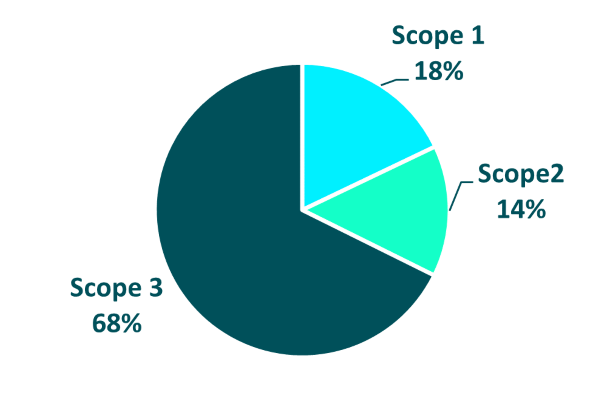
We found that the largest proportion of Scope 3 emissions is the embodied carbon of substrate, and, using our expertise, helped the organisation challenge their business processes with the highest potential for reduction, from raw material through to substrate manufacturing. The embodied carbon of other materials, dominated by solvents, is also a significant contributor. Heat, electricity and direct emissions (Scope 1 and 2) constitute 1/3 of the total; however, the challenges of how to deal with each of these components varies significantly.
Step 2- Stretch your options for your site-level Net Zero pathway
Verco supported the organisation to implement the site-level Net Zero Pathway (Figure 2) to explore all possible interventions from energy efficiency through to decarbonisation technologies.
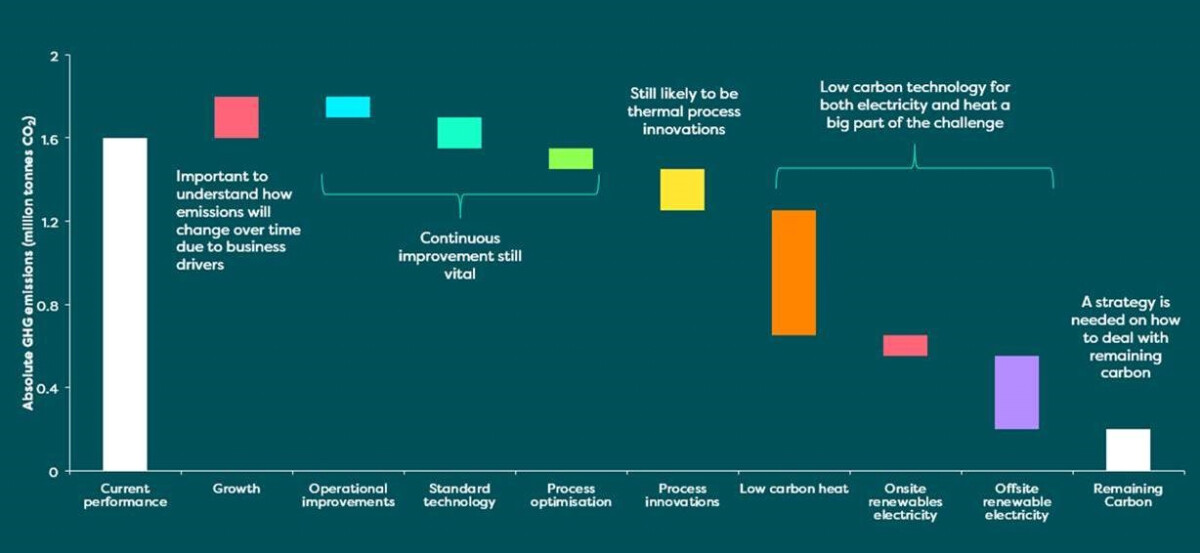
Our engineering team baselined the organisation’s on-site energy consumption and emissions and implemented a rigorous aM&T (automatic monitoring and targeting) system with continuous support to ensure that opportunities are identified early via Carbon Desktop and deviations are acted upon immediately.
Verco’s engineering team have assisted the implementation of efficiency improvements with the view to reducing heating and electricity demand, and this is often beyond the typical “low-hanging fruit” opportunities. Specific focus areas, among others, including compressed air sequencing and baseload usage at idling plant and cooling plant efficiency improvements. Significant potential lies in heating optimisation and more specifically in optimising thermal oxidisers, baseload steam consumption coupled with managing the printing press heating circuit. HVAC and lighting optimisation are included in the “no-regret” options for energy efficiency.
Efficiency improvements would only go so far and therefore the organisation is looking beyond to process innovations, low carbon heat and electricity generation to tackle the remaining Scope 1 and 2 emissions. Verco have carried out a Screening Assessment to understand feasible site options for recovering raw materials, installing renewable electricity and heat generation to match site demand and the potential for growing energy crops. This has helped the organisation narrow down the options with relatively little effort. Available market instruments for reducing market-based emissions coupled with site electrification is also being assessed as an alternative option.
Step 3- Challenge your supply chain and focus on the ‘’big-hitter” interventions to generate momentum
Focusing on the embodied carbon of substrate and other key materials, such as solvents and inks, has generated business cases for significantly reducing the impact of the supply chain to the organisation’s Scope 3 emissions. In addition, it has driven and engaged the entire business in discussions with suppliers which would not normally take place, generating cost efficiencies at the same time. Whilst there are still opportunities to optimise the supply chain, the key areas for cost-effective Scope 3 emissions reduction include:
- Alternative sourcing of raw materials
- Optimisation of transport routes and sourcing to significantly lower transportation emissions
- Raw material recovery on site
- Increase of in-house production of materials vs. external supply
How far can these initiatives go and over what timescale?
While there is still a long way to go, and there are no easy answers, current plans would see the organisation’s carbon footprint reduce by about 1/3 in less than four years. Additional measures and a strategy on carbon insets and offsets are currently being developed with the support of Verco to deal with the remaining emissions.
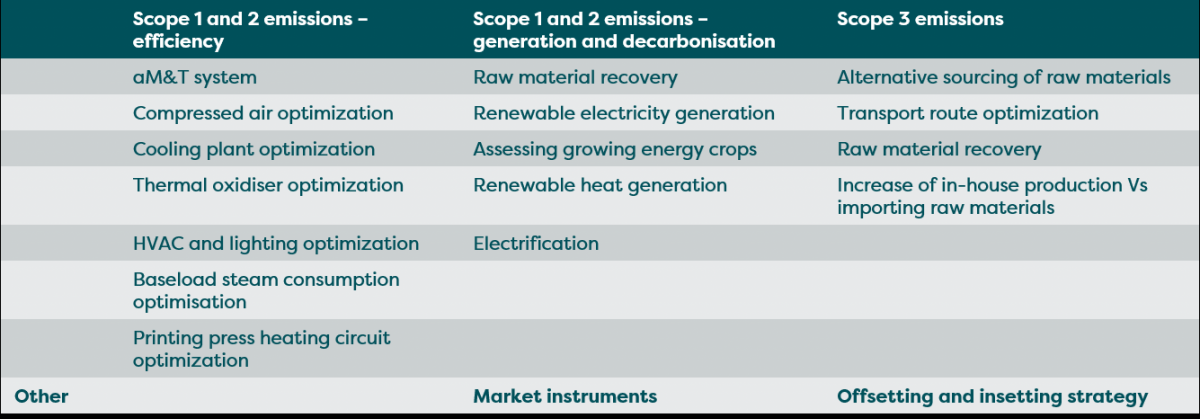
If you want to learn more about what we can do for your business, please read our Net Zero for industry ebook.